1.1 What is Concrete Masonry?
Introduction
Concrete masonry construction (or as it is more commonly called, concrete blockwork) is based on thousands of years experience in building structures of stone, mud and clay bricks. Blockwork masonry units are hollow and are filled with concrete and allow for the integration of reinforcing steel, a feature essential for earthquake resistant design.
Concrete blockwork provides a structural and architectural advantage in one material and is recognised worldwide as a major contributor to the construction and building industry.
Types of Concrete Blockwork
The workhorse of concrete masonry has traditionally been stretcher bond blockwork forming structural, fire and acoustic functions from residential to large commercial buildings as well as the special use in retaining walls.
With the introduction of coloured masonry Architects and Specifiers are using Architectural Masonry in more commercial and residential applications.
Using the various textures of Fair Face, Honed and Splitface is adding a lot more variety to the features of the wall.
There are also masonry blocks that include polystyrene inserts which provide all the structural benefits of a normal masonry block with the added advantage of built-in insulation.
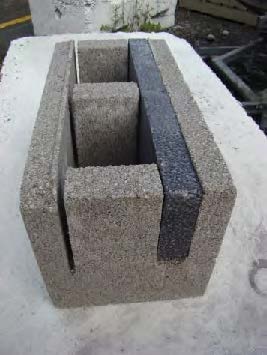
Building with these blocks removes the need for additional insulation – providing the added design flexibility of a solid plastered finish both inside and out.
The word “Concrete Masonry” also encompasses a wide variety of products such as, brick veneers, retaining walls, paving and kerbs.
Brick veneers are available in a range of sizes and colours and also have a large module range and can be splitface or rumbled.
Retaining wall blocks cater from the heavy duty type applications down to the DIY ornamental walls around garden beds. The splitface types give the appearance of natural stone.
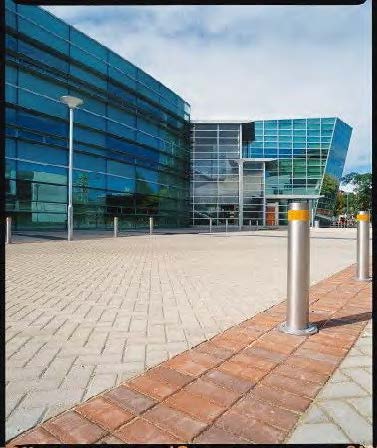
There is a wide variety of paving available in different colours and shapes and textures for both residential and commercial applications. Bush hammering and honing are also options as a secondary process which adds variety to the textures.
Flagstone paving brings additional terrazzo style finishes to the range of products the concrete industry can supply.
Permeable paving and grass pavers are also available for use in residential and commercial applications.
There are some major advantages for permeable paving especially in a world which is far more conscious of the sustainability of our environment.
Advantages of Permeable Paving
- Improved water quality from runoff by filtering out contaminants.
- Improved hydrological response of stormwater peak flow by holding and releasing in a controlled manner.
- Providing amenity/landscape feature, especially when different coloured pavers are used.
- Allows utilizing the paving area for treating its own stormwater and therefore does not require ant additional land areas outside the paving area to treat stormwater runoff.
- Increases the impermeable footprint of a site as the driveway, carpark or patio is treated as a permeable surface.
- Can be manufactured in various formats and still maintain commercial strength and limited maintenance.
Formpave is a proprietary storm water source control system which allows heavy rain to infiltrate through a permeable concrete block paved surface into a unique sub-base before being released in a controlled manner into sewers or water courses.
Formpave Storm water source control systems and Aquaflow permeable paving products are suitable for use on carparks, industrial estates, retail centres, pedestrian areas, domestic drives, motorway services, airport service areas and aprons, garages and other heavy duty operations and are discussed more fully in Section 7 of this Manual.
Heavy Duty Commercial Paving
Commercial paving can be manufactured with increased strength to resist heavy axial and point loads in heavy duty applications such as Airport aprons, container yards, wharves and sawmill processing yards.
The product can also be delivered in a herringbone pattern to enable a machine laying process which is far quicker in areas between 5,000 m2 to 20,000 m2
Masonry Block Manufacture
Almost without exception, concrete blocks are now made in fully automatic machines. Raw materials are stocked in separate bins near to the mixer which is so arranged that concrete is fed to the block making machine either by gravity or mechanically.
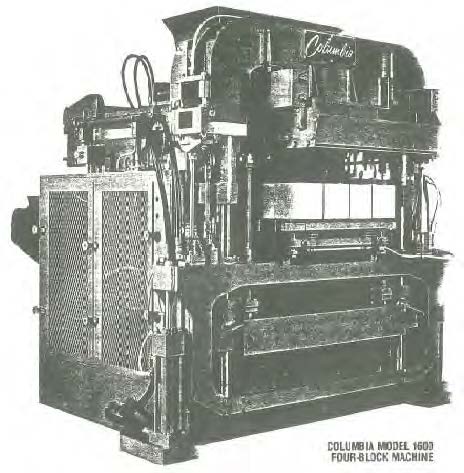
Columbia Model 1600 Four Block Machine
Figure 34: Columbia Model 1600 Four Block Machine The concrete mix design is such as to produce the desired properties in the finished units as well as being properly workable for filling the moulds, pressing, vibration, stripping and moving of the fresh blocks to the curing chambers.
Concrete used in block making is of a very dry cohesive mix designed for moulding in conjunction with powerful vibration simultaneous with compression while in the mould.
In most systems the blocks are extruded from the moulds in a downwards direction, being pushed by a multi-plunger type head mechanism fitted with stripper shoes. These heads, like their matching moulds, are specially shaped to suit each respective block type.
The mould bases are heavy steel plates, or pallets. A steel pallet is used for each new moulding cycle and acts as a supporting tray for the newly moulded blocks in their removal from the moulds and the passage through the curing process. Blocks are removed from the steel pallet at the dispatch station which returns the steel pallet to the block making plant.
Curing
For structural masonry the ‘green’ blocks, after demoulding, are mechanically conveyed and loaded in racks for curing, usually in large insulated chambers.
Once the ‘green’ blocks are in the chamber, steam at atmospheric pressure and above 70°C is introduced into the chamber, thereby accelerating hydration – the chemical reaction between water and cement which causes hardening. This allows blocks to be packaged the day after moulding.
Other masonry products may have alternative curing processes which do not involve the use of steam or accelerated curing resulting in energy saving.
Secondary Processes
In some instances, blocks are passed on to other machines for further processing, e.g. concrete bricks for rumbling, which gives random rounded edges to the units, solid units for splitting into split face blocks or honing which removes the top 2-3 mm of the surface to expose the matrix and the aggregate, which gives the appearance similar to a “terrazzo” product.
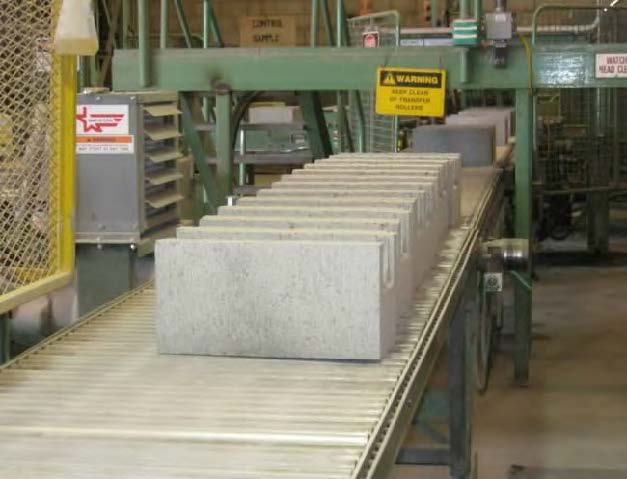
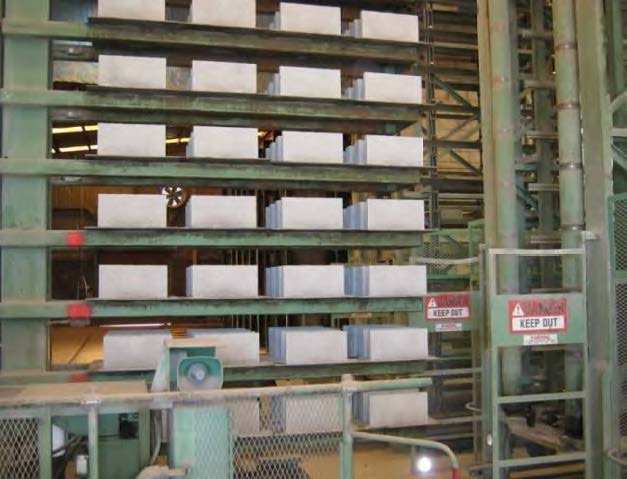
Packaging and Handling
Following curing the blocks are mechanically conveyed to the “cuber”, which strips the steel pallet, binds the blocks into “cubes” usually 1.2 x 1.0 in plan, on wooden pallets. These “cubed” pallets of blocks are transferred to yard storage and eventually to the construction site. Factory stocks are usually stored out of doors and moved by gantry crane, mobile crane, fork-lift truck or cranes mounted on delivery trucks. Such crane-fitted trucks are usually used for deliveries to the construction site.
Quality Control and Testing
All aggregates and cement are subject to checking and the design and proportioning of mixes are closely supervised. Machine controls, moulds, cores and height mechanisms are regularly checked to ensure dimensional accuracy.
Prior to cubing or further processing, units are subjected to a continuous visual inspection. Blocks of sub-standard appearance are rejected and removed. At this time blocks are taken at random from the conveyor run as specimens for testing in compliance with AS/NZS 4455. A suite of testing procedures for masonry is contained in AS/NZS 4456. The resulting consistency of product provides a dependable building material.
Advantages of Concrete Masonry
Concrete masonry stands almost alone as a material that can meet structural and architectural requirements within itself. It is predictable, and therefore reliable. It gives a sense of security.
The nature of concrete provides permanence, high fire and acoustic resistance and minimum maintenance.
It is available in a wide range of texture, shape and colour; and in units ideally suited for vertical, horizontal or sloping building elements and surfaces.
Concrete masonry lends itself to the development of exciting and efficient architectural and engineering forms and finishes. The versatility of concrete masonry, perhaps more than most other materials, enables it to meet the ever changing demands of a progressive society.
Concrete masonry walls have the ability, if positioned correctly, to capture free energy from the sun “thermal mass” and will help with the thermal efficiencies of a house or building.
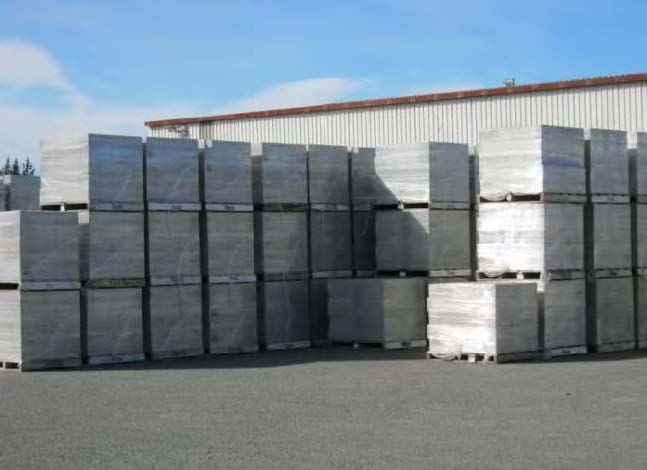
Cubed Pallets of Concrete Blocks
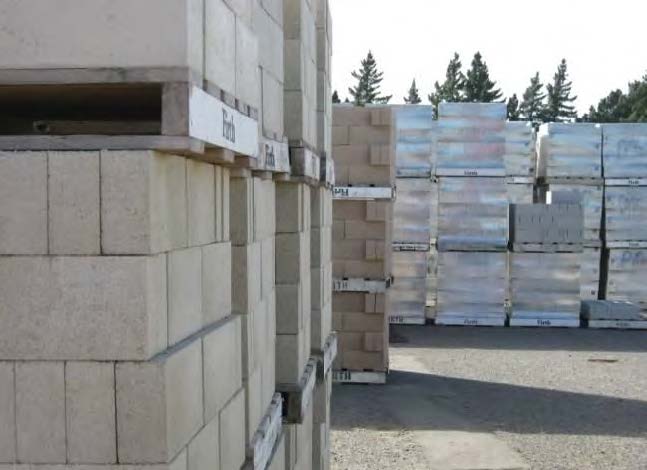
CONTENTS
- General
1.1 What is Concrete Masonry?
1.2 Concrete Masonry Wall Units
1.3 Modular Wall Masonry
1.4 Mortar and Mortar Joints
1.5 Blocklaying
1.6 Masonry Trades and Registration of Masons
1.7 Specifications for Concrete Masonry Wall Units
- Properties of Concrete Masonry
2.1 Fire Resistance
2.2 Weather Resistance and Surface Coatings
2.3 Thermal Performance/Passive Solar Design
2.4 Acoustic Performance
- Construction Details
3.1 Basic Masonry Construction
3.2 Reinforcement for Masonry
3.3 Wall Construction
3.4 Compressive Strengths of Masonry Prisms
- Reinforced Masonry
4.1 Design of Reinforced Concrete Masonry Structures
4.2 Standard Specifications for Concrete Masonry Buildings Not Requiring Specific Engineering Design
4.3 Masonry Buildings Not Requiring Specific Design
4.4 Design Publications
5.1 Veneer Walls
5.2 Concrete Bricks and Walls Ties
5.3 Specification for Concrete Masonry Bricks
5.5 Veneer – Stack Bond
- Specific Constructions
6.1 Masonry Retaining Walls
6.2 Garden Walls
6.3 Control Joints
- Pavers
7.1 Concrete Segmental and Flagstone Pavers – Guide to Specifying
7.2 Segmental Paving Design and Construction
7.3 Permeable Interlocking Concrete Pavements